Case Study
How Siemens streamlined and centralized their global labeling with Loftware
Share
The Siemens Digital Industries factory in Chengdu, China, initially relied on a custom-built labeling system. However, the increasing demand for QR code printing and the need for system upgrades prompted both the Chengdu factory and its sister facility in Hamburg, Germany, to adopt the IRIS platform. With the implementation of Loftware’s solution, Siemens was also able to eliminate monthly communication errors across more than 70 printers, further enhancing operational efficiency.
Download this case study to learn more about how Loftware helped Siemens Chengdu achieve key results such as:
- Easier and more user-friendly label design
- Standardized and secure label management
- Support or complex label scripts
- Remote printer monitoring
- Complete print history
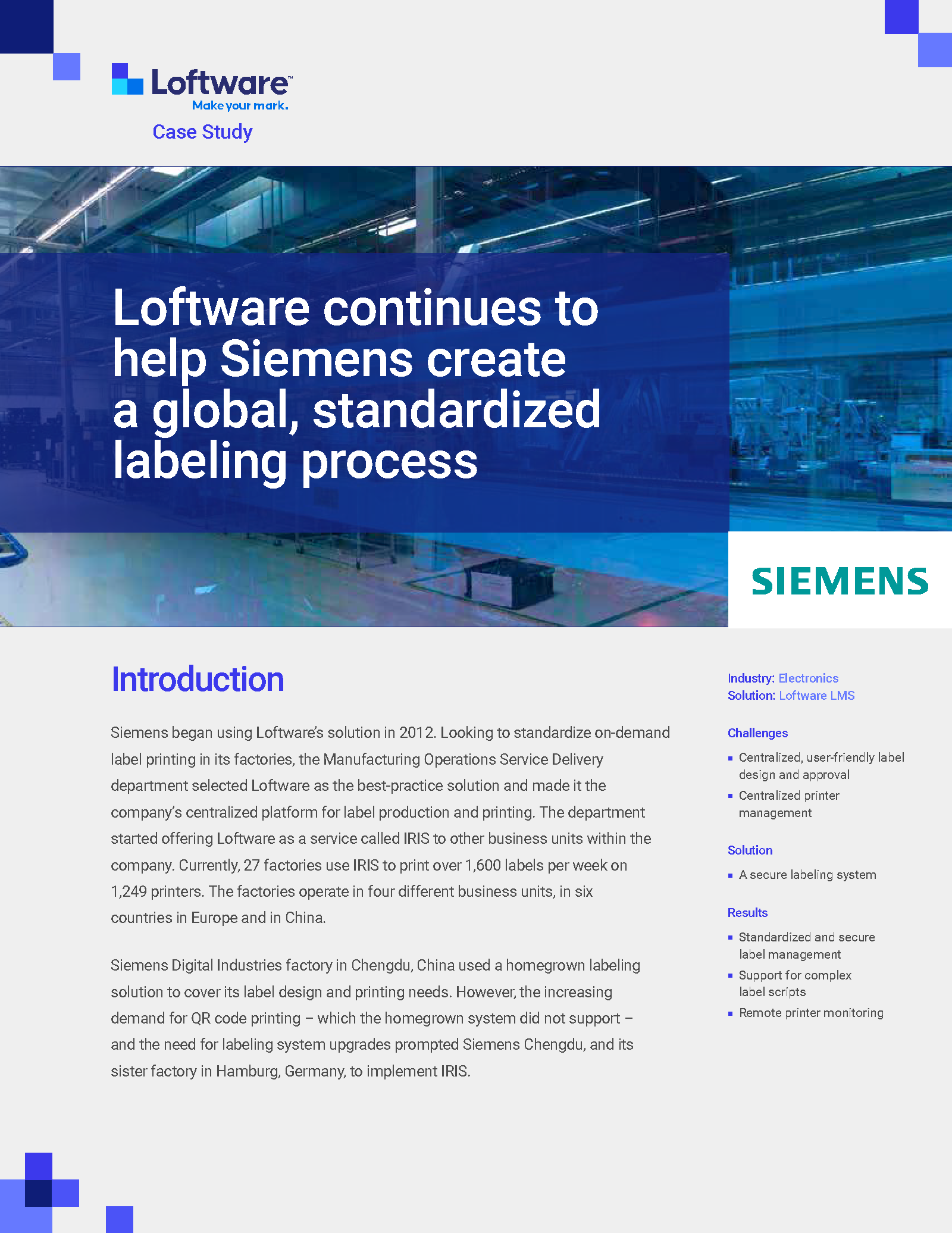